If you travel through any major wine or fruit growing region in New Zealand or Australia, you’ll be sure to see FrostBoss frost fans protecting the crops. These impressive fans are used for frost protection for vines, kiwifruit, nuts, citrus and all stone fruit among others.
At night time there is a nocturnal release of heat from the ground which creates an 'inversion layer' of warmer air, which can be found from 10-50 metres above the ground. During a radiation frost, a frost fan is used to draw down the warmer air in the inversion layer and blow it into the orchard or vineyard. The frost fan needs to blow as much air as it can, to the greatest distance possible. The frost fan is angled slightly downwards to pull this inversion layer down to ground level, to protect the crop from frost damage. Frost fans have therefore become an essential tool in most frost protection strategies. Each fan covers approximately 7 hectares of crop.
New Zealand Frost Fans (NZFF) who manufactures the FrostBoss fans, was purchased 10 years ago by Steve Haslett and has continued to grow throughout NZ, Australia and other parts of the world. With its headquarters in Hawkes Bay, the company now employs 50 people in its operation. Outside of NZ, Australia is the next biggest market for their fans.
They currently build in excess of 400 units a year. The fan blades underwent a two year R&D programme in order to create the ultimate performing blade, which is also quiet. The four or five blade composite blades are fabricated in house and the complete units are assembled in NZFF workshops, including fabricating the 10m tall towers, reconfiguring the engines for the application and building the clutches and controllers.
NZFF use Perkins 1106D-70TA engines in some of their units and they recently celebrated a milestone of importing 1,000 Perkins engines into NZ, purchasing them off the NZ Perkins dealer, TDX Ltd. These engines are an inline 6 cylinder, rated at 150hp @ 2,400rpm and they are running at 1,750rpm in this particular application. The blades are pitch harmonised with engine output to achieve maximum fuel efficiency.
Steve Haslett advised that they choose Perkins engines because “The Perkins engines are robust and reliable. The machines do low hours, but they must fire up first time every time when needed. The application means that the use of the engines is intermittent, but hard running when needed, they may run hard for up to 12 hours”. Steve further added that “TDX are very easy and good to deal with and he is very happy with the service he receives from them and the Perkins support team”.
NZFF have service centres in the main growing areas of New Zealand and Australia with a service team covering the country and have 9 specialist service trucks (one more being added to the fleet this year) with elevated platforms in order to check the blades, and service gearboxes, and drive-shafts.
Refits and rebuilds are also a growing area of the business and NZFF currently upgrade about 100 fans each year, including replacing blades, gearboxes, controllers and solar panels.
The fans are able to be remotely monitored 24/7 via internet monitoring, which is also smart phone compatible. The monitors operate via a cell network and are used to check fuel levels, battery voltage, and they will monitor the canopy temperatures and the fans operation through a frosty night, providing information on the fans performance, efficiencies etc. The monitors enable historical data to be collected and trends established and analysed. The temperature sensors are wireless temperature probes that sit at canopy level and the controllers can be set to auto start and stop the fans at operator pre-set temperatures. Generally the fans are triggered into action when the air reaches 0.5°C. This can be adjusted if growers wish to. The fan blades pull down the warmer air and spread it across the crop canopy.
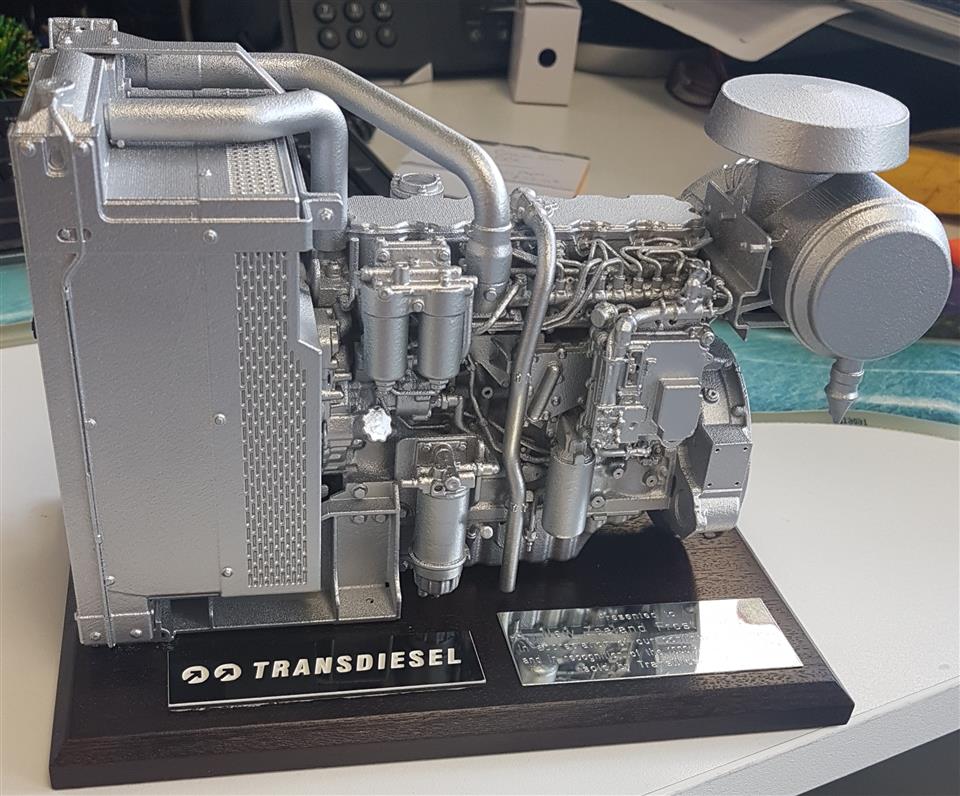
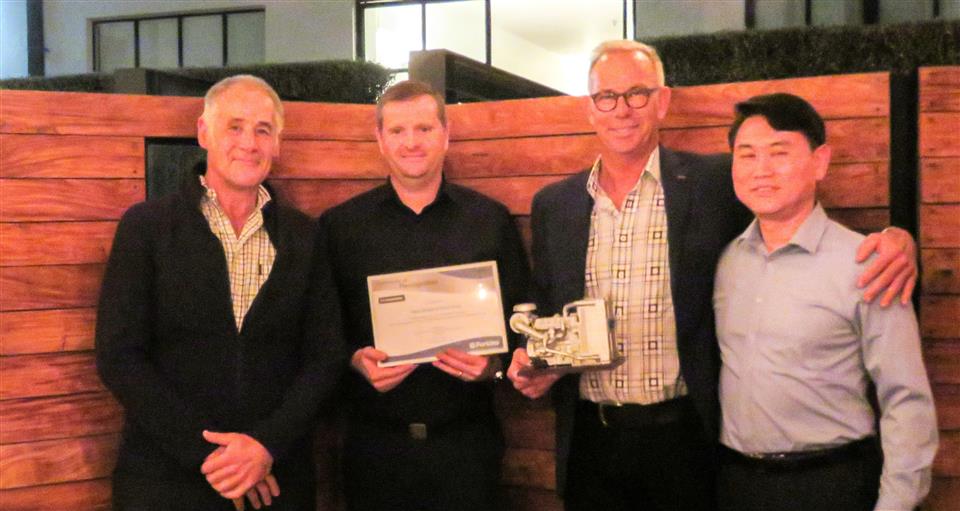